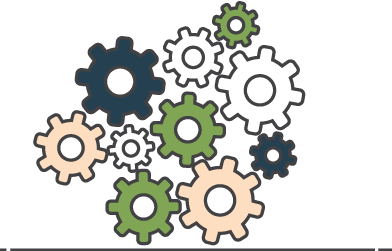
The Project
The client had built a successful, multi-location operation providing its services to many of the world’s largest automobile manufacturers. Their offerings span across the logistics process: In U.S. ports and railheads, the company inspects automobiles for damage as they are loaded and unloaded from overseas and domestic transports. They collect detailed part-level exceptions for each, including photographs and repair estimates, to support claims to the carrier on behalf of their clients who include BMW, Ford, Volvo, and Chrysler.
They also have operations directly supporting the domestic manufacturing plants, providing a variety of logistics support including storage, damage repair, and transportation.
The company engaged Fox Wyndrum Associates to develop integrated systems to help it contend with high-capacity data collection, consolidation, and exchange. It needed to reduce the inherent redundancies of its disparate systems and expedite required reporting to its automobile manufacturing clients.
The Challenges
Any given vehicle, as identified by its 17-digit Vehicle Identification Number (VIN), may pass through the company’s system multiple times as it is moved into and out of storage en route to dealer destinations. The collected data is used to file claims, report storage activity, and bill the manufacturers for services. There are few industry-wide standards for the data set collected, and so the company needed to map its data model to a multitude of external systems and protocols in order to meet its obligations and efficiently report to and bill its clients.
Some of the physical locations of the inspections and other services conducted by the company were outside of communication range, requiring offline processing, a mobile application, and data uploads.
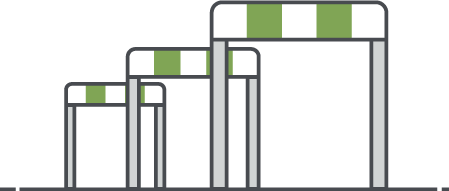
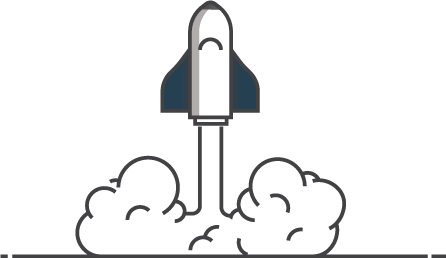
The Solution
Fox Wyndrum Associates Inc. developed several integrated yet independent applications for the company’s different business units.
Vehicle Inspection Management
The inspection process starts with offline data collection using handheld devices, where motor vehicles of all kinds are examined for transport damage. Exceptions are tracked down to the part level using client-defined damage, cause, and repair codes, along with accompanying photos. The data is uploaded into a Survey Management System that lets users review, edit and price surveys for repair estimates. Completed surveys are transmitted to their client’s disparate systems using custom data-mapping matrices which can be maintained by the company. Extensive reporting allows the company to customize every survey to process to its clients’ wishes.
Vehicle Storage and Maintenance Activity Management
The company manages a number of offsite storage facilities for domestic auto manufacturers, providing storage and maintenance services for the vehicles. It allows the company to trace and invoice for all activities, from receipt to discharge, including cleaning, repair, labeling, sorting, and creating mix loads for transport to dealerships. It includes a space-level locator for every activity for every vehicle for accurate real-time inventory. It includes full inspection functionality as found in the Vehicle Inspection Management. There are many reporting options with customizable content to meet the company’s varying client needs. All transactions flow into a billing module that generates documentation and electronic invoices to clients.
Vehicle Transportation Management
The company is hired to deliver vehicles to dealerships, rail heads, ports, and other storage facilities. This module was developed to track the shipment orders, generate Bills of Lading, and record all activity related to the transportation, and create real-time Proof of Delivery documents. It supports multiple inspections across the process to identify timing and cause for any damage, and identifies shipper, driver(s), recipients, and receipt confirmations. The client can create custom rate tables for pricing and revenue tracking.
Claims Processing
With many tens of thousands of vehicles stored and transported in a given year, the process of managing detailed damage claims with carriers, customers, and manufacturers is an onerous one. Because the system captures highly-detailed activity and inspection data throughout a VIN’s possession, Fox Wyndrum was able to develop a streamlined claims processing module that readily consolidates necessary documentation and repair estimates. The company was able to not only save considerable man-hours by eliminating the manual process, but greatly increased the accuracy of its claim reporting.
The system has fully automated the complex, detailed data collection and reporting across the organization operations, increasing productivity, accuracy, and profitability.
Have a unique business need? Tell us about it!
Do you have a process that doesn’t “fit” an off-the-shelf solution? Do you have disparate systems that need time- and money-saving integration? Contact us today by calling 908-791-0100 or using the form below to schedule a FREE, NO-OBLIGATION conversation to discuss your needs .